Unveiling Dental Burs: Traditional Manufacturing Techniques Explored
Dental burs, tiny yet powerful tools, are essential for modern dentistry, enabling precise carving a…….
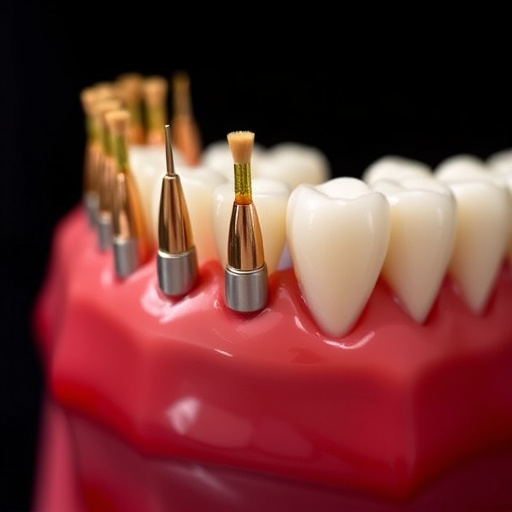
Dental burs, tiny yet powerful tools, are essential for modern dentistry, enabling precise carving and shaping during various procedures. With diverse geometric shapes and abrasives, they facilitate tasks from drilling to crafting intricate tooth structures. Advances in material science have enhanced their durability and performance. These versatile tools come in different designs for specific tasks, such as endodontic treatments or restorative work. Traditional manufacturing methods, involving metal wire/rod processing, ensure quality control but are being supplemented by innovative technologies to further improve precision and efficiency in dental burr production.
Dental burs are indispensable tools in manufacturing, especially for intricate dental procedures. This article delves into the world of dental bur production, exploring traditional methods like hand-crafting and CNC machining, as well as modern innovations such as 3D printing and laser cutting. We’ll unravel the diverse applications of different bur types, dissect quality control measures, and gaze into future trends shaping dental bur manufacturing. Understanding these processes is crucial for ensuring precision and the ongoing development of this essential dental technology.
- Understanding Dental Burs and Their Role in Manufacturing
- – Definition and purpose of dental burs
- – Types of dental burs and their applications
- Traditional Manufacturing Methods for Dental Burs
Understanding Dental Burs and Their Role in Manufacturing
Dental burs are tiny, precision tools that play a pivotal role in modern manufacturing, especially within the dental industry. These intricate devices are designed to cut, shape, and grind various materials with extreme accuracy, making them indispensable for crafting complex dental components. Each bur is crafted with specific geometric shapes and abrasives, enabling precise carving and shaping during dental procedures.
In manufacturing, dental burs are utilized in a range of applications, from sculpting dental restorations like crowns and bridges to creating intricate patterns on tooth surfaces during restorative work. Their ability to execute delicate maneuvers with high precision ensures the creation of custom-fit, aesthetically pleasing dental solutions. With advancements in material science, modern dental burs offer enhanced durability, improved performance, and safer handling, revolutionizing the way dentists practice and patients receive care.
– Definition and purpose of dental burs
Dental burs are tiny, precision tools designed for use in dentistry, specifically for drilling and shaping tooth structures. These intricate devices are a fundamental component in various dental procedures, from preparing teeth for fillings to creating intricate restorations. The primary purpose of a dental bur is to cut through enamel, dentin, or even bone with extreme accuracy, allowing dentists to modify and reshape teeth while also facilitating the insertion of crowns, bridges, or other restorative materials.
They come in diverse shapes, sizes, and designs, each optimized for specific tasks. For instance, some burs are designed for initial tooth drilling, while others are crafted for detailed carving and finishing. The versatility of dental burs enables dentists to navigate complex oral anatomies with ease and precision, ensuring the best possible outcomes for patients.
– Types of dental burs and their applications
Dental burs are essential tools in odontological procedures, offering precise and controlled cutting capabilities. They come in various types, each designed for specific applications. For example, round bur bits excel at drilling and shaping soft tissues, while flat or square burs are ideal for carving and grinding hard structures like enamel and dentin.
The choice of dental bur depends on the task at hand. In endodontic treatments, for instance, specialized burs with tapered points facilitate the removal of pulp tissue without damaging the root canal walls. In contrast, in restorative work, diamond-impregnated burs provide efficient cutting for precision carving during crown and bridge procedures.
Traditional Manufacturing Methods for Dental Burs
In the realm of dental procedures, precision and quality are paramount, making traditional manufacturing methods for dental burs a critical topic. These small yet crucial tools, designed for intricate tasks within the mouth, have historically been crafted through established techniques. One common approach involves cutting and shaping metal wire or rod into the desired form using specialized machinery. This method ensures consistent dimensions and offers control over the final burr’s characteristics.
Additionally, traditional methods often include heat treatment to enhance durability and hardness. The process involves heating the metal to specific temperatures, followed by rapid cooling, which improves mechanical properties. Such craftsmanship has been the cornerstone of dental care, providing practitioners with reliable tools for years. However, with advancements in technology, alternative manufacturing techniques are emerging, promising enhanced precision and efficiency for dental burs.
Dental burs play a pivotal role in modern manufacturing processes, offering precise cutting and drilling capabilities. With various types catering to specific tasks, these tools have streamlined dental prosthetics and orthodontics. Traditional methods form the foundation of their production, but advancements continue to refine the art of crafting dental burs, ensuring better patient outcomes and enhanced clinical efficiency.